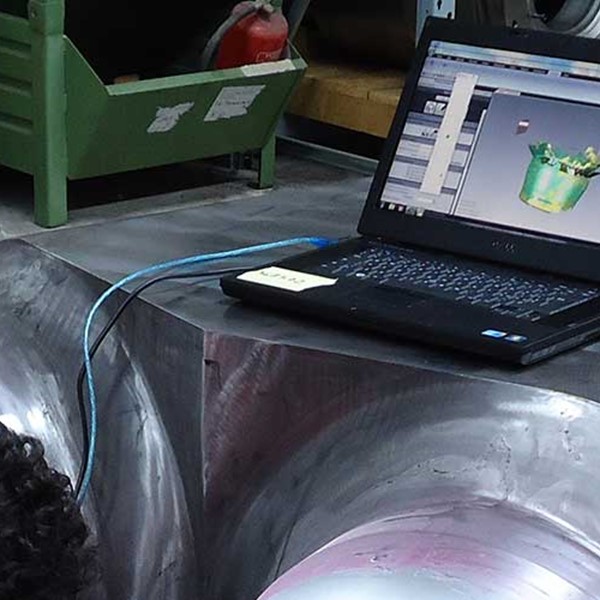
On this page we will delve into:
Weld overlay is a technique used to apply a layer of material onto the surface of a workpiece to enhance its resistance to corrosion, wear, or high temperatures. This process involves welding a protective metal layer onto a base material, improving its properties and extending its lifespan. The process can be performed using various welding techniques, depending on the desired outcome and specific application needs.
Weld overlay is utilized to extend the lifespan of heavily exposed parts by plating their surfaces with more durable materials.
This method is crucial for high-cost components designed for long-term use or for parts that cannot be entirely constructed from wear-resistant materials. It is frequently applied in the petrochemical and power generation sectors, particularly in pipe and manifold coating, and in the aerospace industry to strengthen engine parts.
M.E.G.A. offers a technology that merges two TIG arcs into one powerful arc. The preheated filler wire, heated by an additional current source, enhances efficiency and the fusion profile.
This process enables the adjustment of layer thickness between 1.5 and 3.5 mm, optimizing the amount of fused metal according to stringent criteria, leading to substantial material cost savings. Welding speeds can be optimized between 500 and 1000 mm/min, with deposition rates ranging from 2.5 to 6 kg/h, which is approximately three times higher than conventional Hot Wire TIG technology.
Weld overlay offers numerous benefits that make it a valuable process in various industries.
Weld overlay is utilized across various industries due to its ability to enhance the performance and longevity of components. In the oil and gas industry, it is commonly used for pipelines and drilling equipment, providing protection against corrosion and wear. Power generation facilities employ weld overlay in turbines and boilers to withstand high temperatures and harsh conditions.
The chemical processing industry benefits from weld overlay by applying it to tanks and reactors, enhancing their resistance to corrosive substances. In aerospace, weld overlay is used in jet engines and other high-performance components, ensuring they can endure extreme temperatures and stresses.
The selection of materials for weld overlay depends on the specific requirements of the application. Stainless steel is a popular choice due to its corrosion resistance and strength. Inconel, a nickel-chromium-based super alloy, is ideal for high-temperature applications, offering excellent resistance to oxidation and corrosion.
Cobalt-based alloys are often used for wear-resistant surfaces, providing durability in harsh environments. Nickel alloys are chosen for their toughness and corrosion resistance, making them suitable for various demanding applications. These materials are selected to enhance the performance and lifespan of the base material, ensuring it meets the necessary operational standards.